YOURAPA
Success Stories
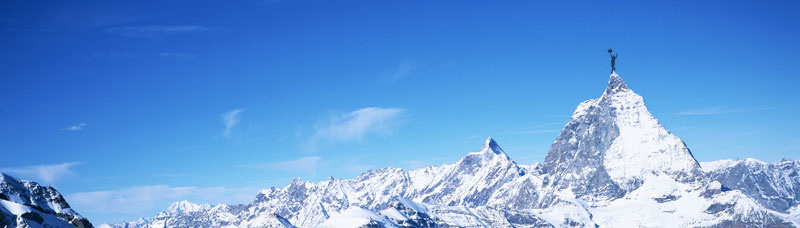
SUCCESS is not what we say or how much we have done. Success is what and how our customers measure us. We are successful when our customers' supply chains continue to maintain high Quality PPM (Parts Per Million), Delivery PPM, YOY Cost Reduction and zero compliance issues from Environmental, Material, and Supply Chain Transparency. We are also successful when we continue to maintain business growth alongside with our customers.

Continuous Improvement is a journey
Challenges:
Capacity Constraint and Long Lead Time
Background:
As part of the continuous improvement actions to improve its overall Capacity and customer Lead Time, Kaizen workshops were conducted.
Tools Implemented:
VSM, Waste Walk, Yamazumi (Line Balancing)
Measurables:
Overall Equipment Effectiveness (OEE), Dock-to-Dock (DTD) Lead Time, Days On Hand (DOH) reduction, Cycle Time Reduction
Results:
40% reduction in overall lead time, 30% OEE improvement

Growth ("make vs buy" of talents)
Challenges:
HR challenges (talent acquisition & labor costs)
Background:
Customer was facing a challenge of not able to hire SQEs and EH&S specialists per hiring plan. APA provided right resources within the required timeframe. In addition, the win-win result was the service fees generated 30% lower cost than the client's internal SQEs and EH&S specialists' total labor costs.
Results:
Fast turn-around of resource readiness, lower labor cost, and experienced SQEs, Cost Management specialists, and EH&S engineers.

Quality drives sustainable business
Challenges:
Customer Dissatisfaction (poor DPPM and QPPM)
Background:
With high Quality PPM and Delivery PPM, the customer was facing financial penalties from its customers. In addition, its air freight costs continued to escalate. A root cause analysis (8D/Fish Bone) was performed.
Tools Implemented:
Standardized work, Control Plan implementation, sub-supply base process improvement.
Results:
within 6 months, 45% improvements in monthly QPPM with no line down. Air freight costs were reduced by 80% within 3 months.

Green supply chain
Challenges:
Environmental Compliance
Background:
The customer needed to ensure its suppliers are in compliance with local regulatory EH&S requirements. On-site audits were conducted, gaps were identified, and action plans for gap closure were performed.
Results:
Suppliers have resolved the non-compliant items, and continued their operations.

Total Value Chain improvement
Challenges:
Production Line Down
Background:
The customer's supplier had change control violation and resulted a mixture of different part levels. SDEs were deployed for containment, issues & resolutions.
Tools Deployed:
8D, DMAIC, PPAP verification & validation
Results:
Root causes were found. The supplier changed in manufacturing processes without communicating with its customer first for an advanced approval. The supplier did not re-PPAP the changed processes. Original manufacturing processes were recovered and entire supplier's production workers went through standardized work and change management workshops. Overall recovery time was less than 48 hours.